半導体製造装置向けポンプ筐体
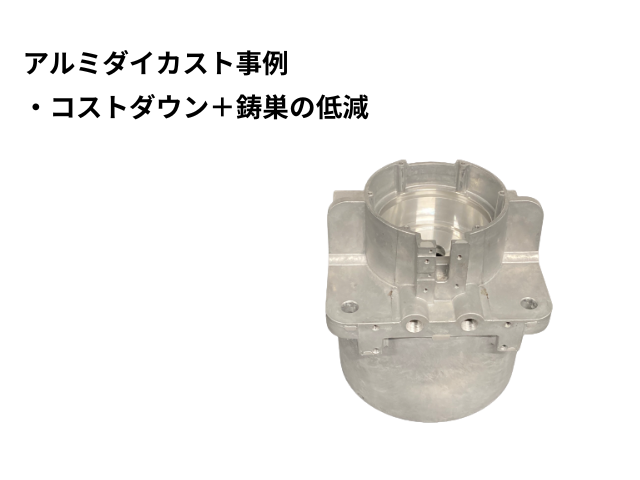
製作部品 | ポンプ筐体 | 業界 | 半導体製造装置 |
---|---|---|---|
寸法 | 215×215×220 | 材質 | ADC12 |
精度 | - | 要求面租度 | - |
納期 | - | ロット数 | 200個 |
対応範囲 | ダイカスト鋳造・機械加工 | 効果 | コストダウン、品質改善 |
工法変換による効果
従来工法
砂型鋳造
提案工法
特許製法 ダイカスト加工
製造リードタイム | 50%短縮 |
---|---|
品質 | 巣の低減 |
当事例の特徴
半導体製造装置に冷却水を供給するポンプの筐体(215×215×220 mm、材質 ADC12)は、従来は砂型鋳物で製造されていました。しかし、アンダーカット部があるため鋳造後に 7.5 mm 以上の大掛かりな追加工が不可避で、その加工代と巣(鋳巣)による歩留まり低下がコストを押し上げていました。しかもこの部位は気密性が求められるため、ほんのわずかな巣でもリークにつながるリスクがあり、品質面でも大きな課題を抱えていました。
そこで当社は、真空引きと局部冷却を組み合わせた特別なダイカスト法を採用し、湯回りとガス抜けを最適化。これにより内部欠陥を極限まで抑え、追加工量を最小限(必要箇所のみの薄削り)に抑制しました。量産立ち上げ時には X 線 CT スキャンで内部品質を可視化した検証データを提示し、全数リーク試験も実施して気密性を保証しています。
結果として、製造コストを従来比 50 %削減しながら、鋳巣起因の不良を大幅に低減。月産 200 個という比較的小ロットでも 30 日リードタイムを維持し、安定供給を実現しています。
そこで当社は、真空引きと局部冷却を組み合わせた特別なダイカスト法を採用し、湯回りとガス抜けを最適化。これにより内部欠陥を極限まで抑え、追加工量を最小限(必要箇所のみの薄削り)に抑制しました。量産立ち上げ時には X 線 CT スキャンで内部品質を可視化した検証データを提示し、全数リーク試験も実施して気密性を保証しています。
結果として、製造コストを従来比 50 %削減しながら、鋳巣起因の不良を大幅に低減。月産 200 個という比較的小ロットでも 30 日リードタイムを維持し、安定供給を実現しています。
当社が提供するサービス
ダイカスト鋳造コストダウンNaviを運営する太陽パーツは、鋳巣を極限まで抑え、コストダウンを実現するダイカスト工法のご提案が可能です。現在の工法にお悩みをお持ちの方は、お気軽に当社にご相談ください。お客様のご要望に最適な工法をご提案いたします。