2023.12.01
石膏鋳造
石膏鋳造の基礎
石膏鋳造とは?
石膏鋳造とは鋳造方法の一種で、金型を使わず石膏で型を作るところに特徴があります。
石膏鋳造の工程
下記、大まかな説明です 。
- 樹脂で製品形状の3Dモデルを製作する
- 3Dモデルをセットした枠にシリコンを流し込みをゴム型を製作する
- ゴム型にシリコンを流し込み反転型を製作する
- 反転型に石膏を流し込み石膏型を製作する
- 石膏型に溶かした金属を流し込み鋳造する
- 石膏型をばらし、鋳造品を取り出し仕上げて完成
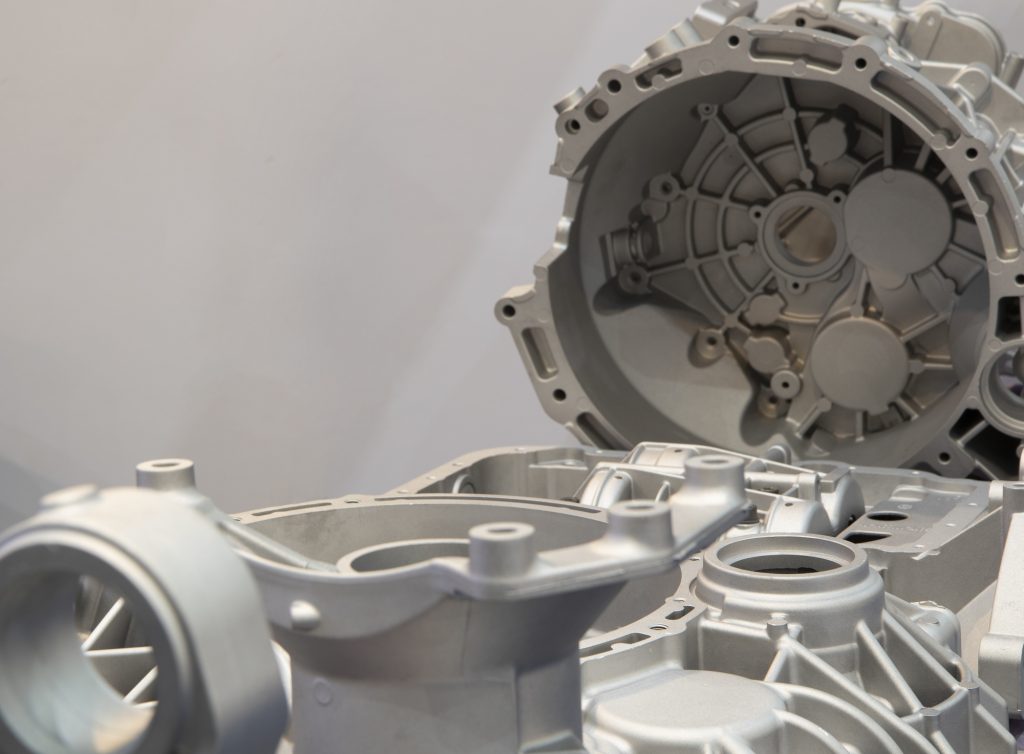
石膏鋳造とロストワックス、ダイカストの違い
石膏鋳造とダイカスト、ロストワックスの比較
経済ロット
- ダイカスト: 3000個以上
- カセットダイカスト: 300~3000個程度
- ロストワックス: 10~500個程度
- 石膏鋳造: 5~100個程度
初期費用
- ダイカスト: 高
- 石膏鋳造 : 中
- ロストワックス: 低
寸法精度、鋳肌
- 対ダイカスト: 同様
- 対ロストワックス: 高い
材質
- 対ダイカスト:
アルミ・亜鉛・マグネシウム等ほぼ同様。ダイカスト用合金であるADC12にも対応可 - 対ロストワックス:
鉄、ステンレス、銅、真鍮等はロストワックスに軍配
形状
- 対ダイカスト:
隅R0や抜け勾配ゼロ、深い溝やアンダーカット形状も対応可能
形状の設計的な自由度が非常に高い - 対ロストワックス:
大物サイズ、薄肉形状に優れる( 投影面積A4サイズだと1.5㎜、 投影面積名刺サイズだと0.7㎜の実績有)
ロストワックスは製法上小物向きなのに対し、石膏鋳造は大物でも対応可
鋳造最大寸法 ⇒ 1200×800×600㎜
石膏鋳造のメリット・デメリット
< メリット >
- コスト:
必要な生涯ロットが100個以下の場合、ダイカストよりも金型費が大きく抑えられるため、トータルコストを抑えられる - 納期:
金型を作らないため金型をつくる工法と比べ納期を大幅短縮できる - 数量:
1~100個程度の小ロットに最適 - 精度:
ダイカストと同等の精度、鋳肌が可 - 材質:
ダイカストと同様の材質で鋳造できるので、ダイカストでの量産前の検証に利用できる - 形状:
砂型鋳物のように中子を使用することで中空形状が可能
減圧装置を用いて金属を鋳型内にいきわたらせるため、ピン角や複雑形状が実現可能
< デメリット >
シリコン製の反転型の耐久が100個程度。大量生産向けではない※マスターモデルは再利用可
アルミ石膏鋳造におけるポイント
下記のような場合にオススメです。
- ダイカスト金型製作前の試作
量産品と同一材料で鋳造するので、形状はもちろん組立確認や強度確認等さまざまな性能評価も可能 実車搭載試験で多用、その他電機や医療機器などでもよく活用される - 生産数量が極めて少ない量産品
コストに大きく影響する金型が不要なので おおよそ5個以上100個未満にコスト優位性を発揮 - ダイカスト本型ができるまでのつなぎ
金型をつくらないため短納期対応が可能 - ダイカスト金型廃棄後のイレギュラーな生産
現物をマスターモデルとして型をつくれるため、昔の製品で現物しかなくても複製可能
石膏鋳造ならCastingNaviにお任せ!
CastingNaviを運営する太陽パーツは、アルミでの石膏鋳造に対応しています。ロストワックスとは違うメリットがある石膏鋳造で様々なご提案も可能となっております。
二次加工や表面処理まで対応いたしますので、小ロット生産や短納期での製造をご検討の方は、お気軽にご相談ください。
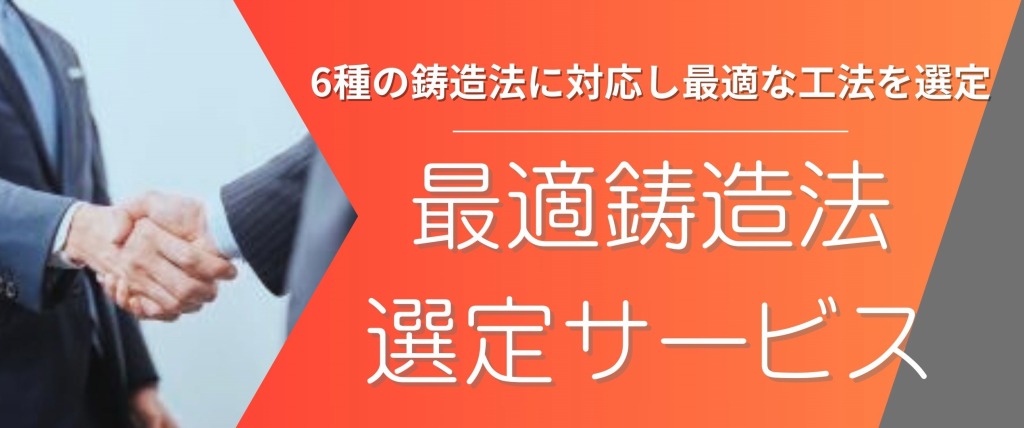