ダイカスト金型の設計・製作のポイント
みなさん、こんにちは!
「ダイカストコラム」です。
今日はいよいよ金型についてお話ししようかと思います。
「金型」って言葉は、よく耳にすると思いますが、どんなものかって
現物を見た事のある人は、それほど多くはないのではないでしょうか?
金型とは
製品によって様々な金型というものが存在します。
みなさんがもっとも目にするプラスチック部材も金型を使用しますね。
ところがプラスチックの種類や製品形状で金型も複数のタイプから選択されます。
まず、最も多いのが「射出成型」用の金型。
熱可塑性溶樹脂を溶かして製品形状のキャビティに流し込んで、冷まして製品にするタイプです。
熱硬化性樹脂の場合は、逆に硬化温度に金型を温めておきます。
他には、PETボトルなどを作る「ブロー成形」用の金型
ゴム部材などを作る「コンプレッション成形」用の金型などがあります。
その他にも、金属板に穴を開けたり、曲げたり、切ったりするプレス製品の金型もありますね。
これも単発抜きから、複数の金型を並べて順番に加工して行く順送とという方法があります。
では、「ダイカスト」の金型ってどんなの?という事ですが、
プラスチックの射出成型金型に似ています。
溶けた金属を製品形状のキャビティに流し込んで、冷まして製品にするタイプですね。
そもそも、この「ダイカスト」という名称が名は体を表しています。
「ダイ」=Die=型、金型
「カスト」=Cast=流し込む、放り込む
つまり、「型に流し込み、製品を作る」と意味になりますね。
「・・・プラスチックでもいっしょじゃん!」という突っ込みはさておき。
ダイカスト金型と射出成形金型の違い
金属を成形するダイカスト金型は、プラスチックの射出成形金型と大きく違う所があります。
1、成形温度が全く異なる
プラスチックの成形温度はせいぜい200度です。ところがダイカストの成形温度は、
700度にも達します。
もちろん金型も金属製ですから熱が加わると線膨張係数に応じて、金型自身も伸び縮みしますね。
常温を25度としてプラスチック成形の200度なら、金型10mmで約0.02mm伸びます。
20ミクロンですね。
ところがダイカストの700度なら、金型10mmで約0.078mmも伸びます。
そうです、78ミクロンです!
製品の精度出すのは、技術者のノウハウで何とかなるとしても、金型全体の構成も
よくよく考えないと簡単にいかない事がわかると思います。
2、金型表面処理
ダイカストの成形温度が非常に高い事がわかったと思いますが、金型そのものも
この温度では劣化が激しいものです。
ですから、溶けた金属が接触する部分には、その高熱に耐えて寿命が長くなる様に
コーティングをする事が一般的になって来ました。
コーティング方法はプラズマ反応を利用した、PVDセラミックコーティングが主流です。
これによって非コーティングよりも約3倍も寿命を延ばす事ができるのです。
3、成形方法
ダイカスト成形と一言で言っても、鋳造方法にも種類があるのです。
・ノーマル鋳造
・真空鋳造・・・キャビティ内を真空引きして鋳巣を減らす方法
・PF鋳造・・・キャビティ内に酸素を充填させて鋳巣を減らす方法
・スクイズ鋳造・・・縦型で溶けた金属を下から上に射出してガスの混入による鋳巣を減らす方法
上記以外にも、ダイカストメーカさんは各社で特殊な方法も編み出しています。
この成形方法の違いによって、金型の材質、方案(金型に溶湯を供給するための流路や、
金型キャビティ内の空気を排出する通路など、金型の各要素を設計すること)、
トリム方法(鋳造のために製品にくっついた余分な部分を除去すること)など全てが異なります。
「太陽パーツ」では、このうちノーマル鋳造と真空鋳造の2種類を対応しています。
ダイカスト金型における設計のポイント
それでは、いよいよ設計しましょう!
設計は金型サイズの決定にはじまり、各製品のパーティング、ゲート、押出し位置や数、そして
仕上げ機械加工の必要な場所、冷却システムなど、全てを加味して最も精度が高く、早く、安くできる型割や
金型構成をクライアント設計者の意向を聞きながら決定して行きます。
このときに、太陽パーツ特許工法である「カセット・システム」が適用できるかを判断します。
適用できれば、「な、な、なんと金型費約50%!」・・・やっす!
いざ、設計というわけですが、型物には必ず収縮率というものが付きまといます。
「1、成形温度が全く異なる」で書いたように、金型は鋳造時にとっても伸びます(大きくなる)。
でも、製品は冷却されて縮みます。
いやー、めんどくさい!
でも、ここが金型設計者の腕の見せ所ですね。この伸び縮みを製品の部分部分で経験とノウハウで
計算して、金型図面に反映させていきます。
つまり、金型キャビティの図面は製品図面の反転だけでは済まないんですね。
ダイカスト金型における製作のポイント
ではでは、金型を作っていきましょう。
まあ、ここを訪れてくれている方々は、何で削って、何で穴開けてなんて説明は
「釈迦に説法」でしょうから致しませんが、ダイカスト用の金型鋼は、プラスチックのそれよりも
硬い材料を使います。
ですから、加工機もそれなりに対応出来る大型のものが必要になります。
そして、削るだけなら、今ではNCですからプログラミングしてやれば
機械任せでそれなりにやってくれます。
ここで大切なのは、仕上げ加工です。
機械加工だけではどうしても切削痕が残りますから、その表面を滑らかに磨きあげる必要があるんです。
こればっかりは、ロボットに任せるわけにもいかず、技能者の腕の見せ所です。
仕上げの磨きの出来次第で金型そのものの出来栄えが評価され、製品の出来栄えにも
直結します。
長年ダイカストの金型製造から鋳造、製品仕上げ加工まで、一貫して生産できる太陽パーツでは
製品の良し悪しもダイレクトに検証できますから、金型での課題もすぐにフィードバックできちゃいます。
つまり、金型設計も金型加工も金型仕上げ磨きの技能者の熟練度は他社さんに比べても
劇的に早く、濃度の濃い内容をノウハウとして蓄積しています。
その上、カセット・システムで対応出来る製品であれば、ベース型を太陽パーツ資産を使うため
お客様にはキャビティ費用だけで済みますし、型の成形機乗せ換えもキャビティの交換だけで済むため
多品種小ロット製品のダイカスト化もお手の物です。
実際の製品事例①:医療機器用固定板
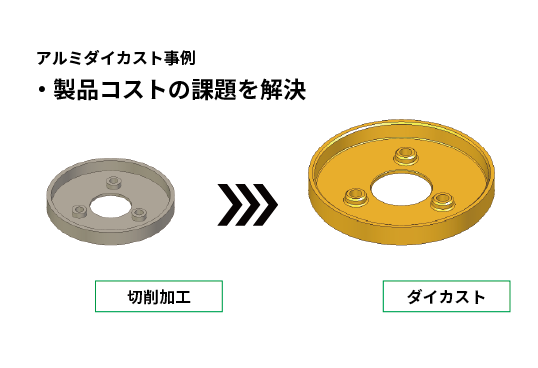
こちらは、医療機器に使用される固定板について、切削加工から特許製法のダイカストに工法変換した事例です。
従来はロット数が少なく切削加工にて製作していましたが、増産に伴いコスト削減と製造リードタイムの短縮が必要でした。
そのため、ダイカストへの工法変換をご検討されましたが、金型費用がネックとなり、断念されていました。
そこで当社は、金型費用が従来の1/2になるダイカストカセットシステムを提案しました。
ダイカストカセットシステムを使用することで増産後の50個/1ロットという小ロットでも十分に投資回収が可能であり、
ご発注頂きました。生産サイクルも短く、製品単価の削減と製造リードタイムの短縮を実現しました。
実際の製品事例②:アミューズメント機器用フランジ
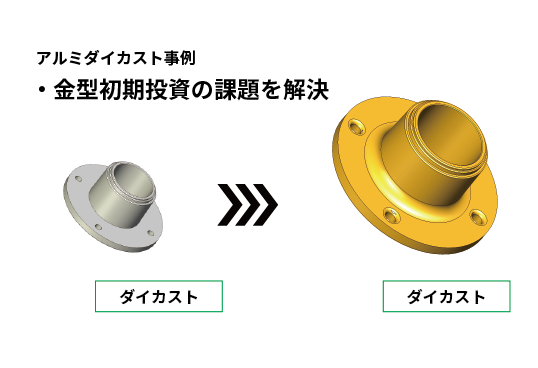
こちらは、アミューズメント機器に使用されるプランジャーについて、従来のダイカストから変更し、
当社の特許製法であるダイカストカセットシステムにて生産を行った事例です。当プランジャーは限定商品であり
3200個の生産と決定しており、初期コストを抑えて生産を行うことをご要望されていました。
他の製品では従来のダイカストを用いて生産されていましたが、金型費用が高くなるダイカストでは投資対効果が十分ではなく、
金型費用を従来の1/2に抑えることができる当社にお声かけ頂きました。
ダイカストカセットシステムでは、従来のダイカスト金型と異なり、特許技術により金型費用を1/2に低減できます。
3200個の限定生産でしたが、十分に投資対効果を見込めることから、当社にてご発注頂きました。
実際の製品事例③:医療機器用薬液排出部樹脂タンク用カバー
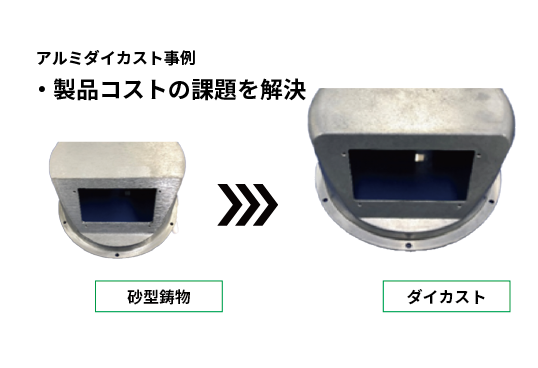
こちらは、医療機器に搭載されるカバー薬液排出部樹脂タンク用カバーの生産工程を、砂型鋳造から当社特許製法の
ダイカストに工法変換した事例です。
従来、砂型鋳造により製作していましたが、生産数量の増加に伴い、製造コストを低減したいというご要望を頂戴しました。
また、砂型での鋳造にて製作すると平均的な肉厚が5mm~6mmと厚肉であり、強度過多で質量が大きい点も問題となっていました。
当事例のお客様は、精度向上・薄肉による軽量化のため他社ダイカストメーカー様にお声かけされたことも
あったとのことですが、初期コストが高く工法変換を断念されていました。
そこで、当社の特許製法であるダイカストカセットシステムにてご提案しました。
当社のダイカスト製法は、従来のダイカスト金型と異なりキャビティーのみの製作となるため、金型費用を1/2に抑えることが可能です。
初期コストが割りに合わないという点で、ダイカストへの工法変換を躊躇されていた当事例のお客様の工法変換が実現できました。
最後に・・・
「この程度のロットじゃ、、、」「ダイカストは金型高いからなぁ、、、」なんてお悩みのみなさん。
ぜひ、一度「太陽パーツ」にご相談ください。
きっと幸せにして見せます!
関連情報はこちら
コラム内検索
関連記事
-
2024.11.24 ダイカストについて
アルミダイカストとアルマイト加工
今回のコラムでは、アルマイト加工について説明していこうと思います。 アルマイト加工って、アルミニウムやその合金の表面に酸化皮膜を作る処理のことなんです。この処理をすることで、耐食性や耐摩耗性がアップする上に、見た目もキレイになるんですね。 […more] -
2024.11.24 ダイカストについて
アルミダイカストにおけるコストダウンのポイント
アルミダイカストを用いることで、大幅なコストダウンを実現できる可能性があります。では、コストダウンを実現するためにはどんなポイントがあるのでしょうか? 3つのポイント アルミダイカストに関して、コストダウンを実現するためには大きく3つのポイ[…more] -
2024.11.24 ダイカストについて
アルミダイカストに使用される合金:ADC12
ADC12はアルミニウム合金の一種で、特に鋳造でよく使われている材料です。 主にアルミニウムに銅を混ぜて作られていて、強度、耐食性、鋳造性に優れているんです。 自動車部品や電子機器のハウジングなど、様々な産業で活躍しています。 ADC12の[…more]