アルミダイカストについて、基礎知識まとめ!
みなさん、こんにちは。
これまで「ダイカスト鋳造 コストダウンNavi」では、ダイカストや各種アルミニウム合金の特徴についてご紹介してきました。このコラムでは、アルミニウムダイカストについて、皆さんにより分かりやすく理解していただくために、カテゴリーごとに詳しくお伝えしていきます。
ぜひ、最後まで読んでいただき、ダイカストの知識を深めてくださいね!
アルミダイカストと鋳造欠陥
ダイカストにおける割れの原因とその対策
ダイカストが割れる原因には様々なモノがあります。
大きく分けると下記の3つに分かれます。
1.製品設計的要因
2.金型設計的要因
3.鋳造(成形)要因
では、「1.製品設計的要因」から説明しましょう。
樹脂の射出成型をご存じの方はたくさんいらっしゃると思いますが、いざダイカストとなると、少々事情が異なって来ます。
まず、金型に流し込む材料がずいぶん違いますね。 金属材料の溶けた粘度は樹脂に比べて、数十万分の1で”しゃぶしゃぶ”なんです。
簡単に言うと、樹脂は「スライム」、金属は「水」みたいなものです。
そして、金属は熱しやすくて冷めやすいので、樹脂に比べて100倍程度の速度で金型に一気に流し込み、高い圧力で保持して固めます。
でも固まった後は、金属の方が樹脂よりはるかに硬いですね。 つまり、少しも変形してくれないので金型から取り出すのもなかなか難しくなります。
ではどうすれば、取り出しやすいか考えてみましょう。
ダイカストのバリについて
ダイカストにバリが発生する原因には様々なモノがあります。
バリについても大きな要因が3つ有るんです。
1.かじりによるバリ
2.型合わせ不具合によるバリ
3.ダイカストマシン選定ミスによるバリ
では、「1.かじりによるバリ」から説明しましょう。
第一話「ダイカストの割れ!」でもお話ししました内容と少し関係があります。
ダイカストでは鋳造材料がアルミなどの金属になりますから、やっぱり硬いんですね。
樹脂成形では、成形された製品は多少なりとも柔らかくて、ちょっとくらいの無理には製品が変形して耐えてくれるんですね。
樹脂は「がまん強い!」というわけです。
ところが、金属になるとそう簡単に融通をきかせてくれません。
つまり、金型の状態に寄っては、離型の時に製品の表面を引っ掻いてしまい、バリに繋がります。
ダイカストにおける巣の原因とその対策
巣はダイカスト特有の現象と言っても過言では無いですね。
表面はきれいなのに、削って見ると「巣穴のオンパレード!」なんて経験があるんじゃないですか?
この巣にも発生原因は以下の様に、実に様々な要因があります。
1.ガス巣
2.巻き込み巣
3.ヒケ巣
4.ゲート巣
では、「1.ガス巣」から原因と対策を解説して行きましょう。
金型へ溶けた金属を注入するとき、この金属からガスが発生するんですね。
これは樹脂の場合にも発生するので、ご存じの方も多いと思います。
ですから、金型には樹脂型同様に、ガスベントやエアーベントと呼ばれるスキマをわざと設けています。
ところが、溶けた金属は樹脂に比べてはるかにシャバシャバですよね。
まるで水のようです。
つまり、高速で金型の中に流れ込みますから、ガスが抜けきれない現象が発生しやすいのです。
取り残されたガスは金属に覆われて、逃げ場を失ってしまい、巣になってしまいます。
チル層の役割と破断チル層の対策とは
ちょっと専門的なお話をすると、ダイカストは溶けたアルミ材料を金型のキャビティ(製品形状のコア)内に射出します。
この溶けたアルミ材が金型に接触する時に、触れた面が急冷される事で、結晶化した物質が析出して固まる層の事を「チル層」といいます。
では、どういった物質が結晶化するかというと、ダイカストでよく使う「ADC12合金」などは,ケイ素量が9.6~12.0%含まれます。
これは「Al-Si2元系合金」の共晶点である12.6%に近いため、アルミ材を溶融することで、溶けたAl元素とケイ素元素が結合して結晶化するのです。
一方、「ADC10合金」などケイ素量が少ない材料では、凝固温度範囲が広がって「デンドライト」(樹枝状固体)が成長した組織になります。
ダイカストの湯まわり不良
まず、一つ目は「ゲート」ですね。
ゲートはできるだけ厚みのある所で、流れる方向に距離がある方が良いです。
ですから、薄くて、目の前に壁のある様な所にゲートを設けると、流れようと思っても狭い所から、広い所には流れにくいですし、壁にぶち当たると、流れる速度も遅くなり、きれいに流れないですよね。
流すのは金属ですから、できるだけ一気に流れてくれないと固まってきます。固まるとさらに流れる道が狭くなってしまいます。
ですから、狭くて細い所は最後に充填されるようにゲート位置を選ばないといけません。溶湯は金型の固定側から入れる事になりますね。
ダイカストのハードスポットとは?
ハードスポットは簡単に言うと鋳造金属を溶かす溶解炉に混入した異物や
溶湯を長時間溶解炉内に保有することで介在した酸化物が金型キャビティ内に
流れ込んで凝固する現象です。
この異物や酸化物ですが、鋳造金属より柔らかければ、それほど問題視される事も無く
スルーしてしまい勝ちでしょう。
ところが、ダイカストで最も用いられるアルミニウムは酸素と非常に新和性が良く、
酸化すると酸化アルミニウム(Al2O3)が生成されます。
Al2O3と言えば、そうアルミナですね。
ご存じと思いますが、アルミナの硬度はステンレス鋼の3倍、ダイアモンドにも匹敵する
硬さがあります。
アルミダイカストと金型
ダイカスト金型の設計・製作のポイント
製品によって様々な金型というものが存在します。
みなさんがもっとも目にするプラスチック部材も金型を使用しますね。
ところがプラスチックの種類や製品形状で金型も複数のタイプから選択されます。
まず、最も多いのが「射出成型」用の金型。
熱可塑性溶樹脂を溶かして製品形状のキャビティに流し込んで、冷まして製品にするタイプです。
熱硬化性樹脂の場合は、逆に硬化温度に金型を温めておきます。
他には、PETボトルなどを作る「ブロー成形」用の金型
ゴム部材などを作る「コンプレッション成形」用の金型などがあります。
その他にも、金属板に穴を開けたり、曲げたり、切ったりするプレス製品の金型もありますね。
これも単発抜きから、複数の金型を並べて順番に加工して行く順送とという方法があります。
ダイカスト金型の特徴
まずは、鋳造するアルミ材料の違いからお話ししましょう。
太陽パーツの扱う特殊なアルミダイカスト材である、「ADC5」「ADC6」、「HT1」 では鋳造温度が700℃を超えてしまいます。
当然、超高温のため高温に強い金型材料でないと寿命が短くなってしまいます。。
この金型材料がまたお高い!通常の材料より3割ほど高価なんですね。
お客様には申し訳ないですが、イニシャル費用が少しばかりお高くなってしまいます。
一般的に使われるダイカスト材料「ADC12」で有れば、鋳造温度が670℃くらいです。
ですから、一般的なダイカスト用金型材料で大丈夫ですね。
例を上げると、金型鋼材では有名な「日立金属株式会社」さま。いつもお世話になってます。
JIS規格の炭素鋼「SKD61」の中でも、一般的なダイカスト材料「ADC12」の金型は、商品名「DAC」を使用します。
一方、「HT1」や「ADC5」「ADC6」の金型では、高温強度重視と謳われている商品名「DAC10」を使用します。
アルミダイカストの材料
アルミダイカストにおける材料の種類
ADC12はAl-Si-Cu合金で、ダイカスト用アルミの中でも湯流れ性、切削性、全てにおいて高いレベルで
バランスの良い材料なんです。
なんと、世の中にあるアルミダイカストの90%以上は「ADC12」で鋳造されています。
特に特殊用途要望が無い限り、全ての産業の全ての部材に適用可能な万能材料と言えますね。
ただ、アルマイト施工性はよろしくなく、Si単結晶との反応で黒化しやすく、
均一な被膜形成が難しい材料なのでアルマイト施工する場合は、耐食性向上など加飾以外の
目的で施すことになります。
亜鉛ダイカストの特徴と素材について
亜鉛材料の特徴には、以下があります。
①何と言っても「重い」!(笑)
重くていいことなんかあるのか?と思われるでしょうが、
上で挙げた製品例を思い浮かべて下さい。
・ドア取っ手が軽いと、、、、、、なんだか安っぽいんだよなぁ。。。
・蛇口のレバーが軽いと、、、、、、水量調整がやりにくいんだよ!
・勝ち取ったトロフィーが軽々、、、、、、うーん、なんだか価値ない。。。
どうですか?重い事にも価値はあるんです。
②金型の耐久性が良い
アルミダイカストでは700℃以上で溶融しないとアルミは溶けてくれません。
一方、亜鉛では400℃で溶融してくれるんですね。
そりゃー温度が低い方が金型の痛みは少ないというもの。
数十万ショットまで金型更新いらずです。
マグネシウムダイカストの特徴と素材について
みなさんもご存じのように、ノートパソコンやカメラの筺体はどんどんマグネシウム化していってますね。それはなぜかというと、何よりも軽くて強いからなんですね。
具体的にダイカスト材料での比重比較をすると、
マグネシウム(AZ91D)=1.8g/cm3
アルミニウム(ADC12)=2.7g/cm3
亜鉛(ZDC2) =6.6g/cm3
どうですか。およそ亜鉛の1/3・アルミの2/3の比重となります。
では、どれだけ強いかをブリネル硬さで比較しましょう。
マグネシウム(AZ91D)=63
アルミニウム(ADC12)=54
亜鉛(ZDC2) =82
アルミより17%位硬いと言えます。「えー、たったの17%だけかよ!」と思われたあなた。ちょっと待って!硬さだけが強さを表す訳では無いですね。いわゆる剛性と言われるやつで考えてみましょう。剛性は3種類の指標から判断されるべきってご存知でしたか。意外と知られていないんですが、紹介しましょう。
アルミダイカストの表面処理
表面処理の代表的な方法は以下の4種類です。
1.めっき
2.アルマイト
3.化成処理
4.塗装
があります。
まずメッキですが、
めっきと言っても多種多様な物が存在する事はご存じですね。
アルミへのめっき性は悪くないので、さまざまなめっき処理が可能です。
ただし、最表層のめっき材の安定した密着性を確保するために
ニッケル下地めっきや銅下地めっきをおこなうことが一般的なんです。
では、代表的なめっきをご紹介しましょう。
電気自動車(EV)とアルミダイカスト
電気自動車に搭載される部品の要件には以下があります。
1.車全体が軽量である事
内燃機関のエンジンに比べて、モータは非力ですし、電池の持ちを考えても最大の負荷である車重は軽いに越した事無いですね。
2.錆や温度特性など耐候性が良い
これは屋外で使用する車ならでは条件ですね。さて、アルミってそんなに良いのか!?
3.一体化
さて、何の事かわからないですね。
詳細は読み進めてもらえると・・・なるほど!となること間違いなし。
4.製造の優位性
これまた何の事か???とにかく読んでみてください!
アルミダイカストに使用される合金:ADC12
ADC12はアルミニウム合金の一種で、特に鋳造でよく使われている材料です。 主にアルミニウムに銅を混ぜて作られていて、強度、耐食性、鋳造性に優れているんです。 自動車部品や電子機器のハウジングなど、様々な産業で活躍しています。
ではADC12にはどんな特徴があるんでしょうか?ADC12には以下の特徴があります。
優れた鋳造性:複雑な形の部品でも高精度で鋳造できるから、自動車部品や電子機器のハウジングにピッタリなんです。
良好な強度:アルミニウム合金なのに、高い強度を持っているので、丈夫な製品作りに役立ちます。
耐食性:酸化アルミニウムの保護層ができるので、錆びにくく、長持ちします。
熱伝導性:熱を伝えやすいので、冷却装置やヒートシンクにも使われることがあるんです。
加工性:加工しやすいので、切削や成形が楽に行えます。だから、製造コストの削減にもつながるんです。
軽量:アルミニウムがベースなので、軽くて強い製品を作ることができます。
これらの特徴から、ADC12は様々な産業で引っ張りだこなんですね。
アルミダイカストのサイズとロット数
大型ダイカストについて
大型ダイカストの特徴をお伝えしておきます。
「大きいと鋳巣がいっぱい入ってるんちゃうの?」という声が聞こえてきそうです。
しかし、ダイカストの巣って、巻き込み巣やガス巣がその多くを占めていますね。
(詳細は「ダイカストにおける巣の原因とその対策」をご覧ください)
つまり、溶けた金属を金型に注入する際に巻き込んだ空気や、発生したガスをうまく抜き出さないと巣ができるわけです。
ちょっと想像してほしいのですが、お子さんがお風呂で水鉄砲にお湯を入れているとしましょう。
ピストル型の細かく入り組んだ筺体に、お湯はなかなかうまく入ってくれませんよね。
叩いたり、ゆすったり、結構大変です。
ところが、ライフル型の容量の大きな水鉄砲には、意外と簡単にお湯が入ってくれます。
もちろん、水鉄砲の場合は湯口の大きさの差があるので、「空気が抜けやすいから当たり前やん!」と思われたでしょう。
その当たり前が、大型ダイカストにも起きているわけです。
ダイカストの試作について
今日は「ダイカストの試作」と題してお送りします。
「ダイカストで試作だと?イニシャルコスト高いのにできるか!」
おっしゃる通りでございます。
で、みなさまどうしてますか?
たぶん・・・・・・
「形状見るだけなら、今なら3Dプリンターがあるんだよ!」
「強度見たかったら、切削で作ればいいんだよ!」
・・・高いから1個作るのやっとやけど、、、(心の声)
「他にも、、、うーーーーん、無いか。」って感じじゃないですか。
そこは太陽パーツにご相談ください。
もちろん、3Dプリンターでも、切削でもできますが、当社では目的に応じて
他の方法も提案させていただきます。
アルミダイカストに関わる設備
ダイカストの鋳造設備
ダイカストを生産するうえで、以下の設備や付帯機器を用います。
〇ダイカストマシン
これはダイカストの中心的な装置で、高圧で金属を圧入するためのものです。主に、亜鉛やマグネシウムに使われる「ホットチャンバー方式」と、アルミニウムに使われる「コールドチャンバー方式」があります。
〇金型
鋳造の型となる部分で、製品の形を作ります。高精度で耐久性が求められるため、鋼材(SKD材)が使われます。
〇溶解炉
金属を溶かすための炉です。溶けた金属は、鋳造機に供給されます。電気炉やガス炉が主に使われ、材質や生産量に合わせて選ばれるんです。
〇射出システム
溶けた金属を金型に射出するための装置です。
〇冷却装置
ダイカストのプロセス後に、金型や製品を素早く冷却する装置です。
これらの装置が一体となって、効率的な生産が可能になります。
アルミダイカストと二次加工
アルミダイカストと切削による二次加工
ダイカストの素材を実際に見て、触ってみたことはありますか? ダイカストの表面は、ロストワックスや鋳物といった他の鋳造品に比べて、意外とキレイに仕上がっているんですよ。
もし、ダイカスト素材のままで問題ない場合は、できるだけ加工をしない方が、製品コストをグッと抑えることができます。 弊社では、JIS規格(日本工業規格)に基づいて、製造・検査を行っていますので、ご安心ください。
アルミダイカストとアルマイト加工
アルマイト加工(アルマイトかこう)って、アルミニウムやその合金の表面に酸化皮膜を作る処理のことなんです。この処理をすることで、耐食性や耐摩耗性がアップする上に、見た目もキレイになるんですね。
アルマイト加工は、航空機、自動車、家電製品、家具、電子機器など、いろんな分野で使われています。特に、美しい仕上がりと高い耐久性が求められる製品にピッタリなんです。アルミニウムの特性を最大限に引き出すための重要な処理技術で、さまざまな産業で重宝されています。
処理の流れは、以下の通りです。
①前処理:まずは、表面の汚れや油分を落とします。
②電解処理:次に、専用の溶液に浸して、電流を流すことで酸化皮膜を作ります。
③後処理:最後に、色付けや硬化処理を行うこともあります。
アルミダイカストを動画で解説
アルミダイカストのメリットや事例、特徴を動画で解説しています。是非ご確認ください。
ダイカストって金型高いから…ちょっと待って!「ダイカスト一体化でコストダウン!」 ~ダイカスト・カセットシステムの優位性~
ダイカスト化によるコストダウン
「こんな大物でもダイカストでコストダウン!」 ~年間400個の部材を板金構造からダイカスト一体成形は~
当社のダイカスト特許製法:ダイカストカセットシステム
ダイカストカセットシステムは、ダイカスト鋳造 コストダウンNaviを運営する太陽パーツが生んだ特許製法です。ダイカストの金型において、製品部分のキャビティーのみを入れ替え、鋳造を行うため、初期コストの削減や段取り替え時間の短縮を実現できます。
これが特許製法「ダイカストカセットシステム」だ!
当社のダイカストカセットシステムを動画で紹介しています。
ダイカストカセットシステムによる工法変換事例!
ダイカストカセットシステムは、金型に関わる初期コストの低減が可能な工法です。そのため、砂型鋳造やロストワックス、切削加工からの工法変換実績を豊富に持ちます。ダイカストカセットシステムを用いた工法変換事例を紹介します。
検査機器用ラックギア
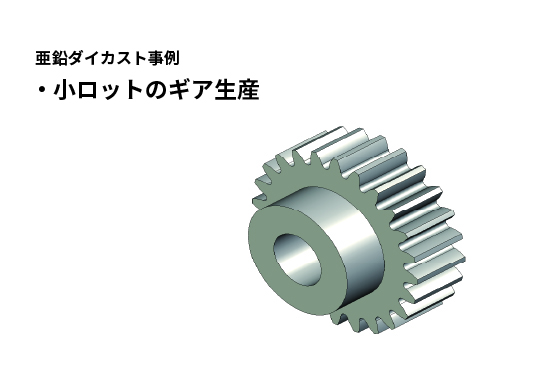
こちらは産業機器で使用されるラックギアです。従来は切削加工により当製品を製作しておりました。コスト面の問題から切削加工からダイカストへの工法変換をご検討されていましたが、金型費用がネックとなっておりました。そこで、金型費用を削減できる当社の特許製法ダイカストカセットシステムへの工法変換をご提案しました。当社の特許製法ダイカストカセットシステムでは、通常のダイカストを比較して、初期コストを1/2に削減することが可能であり、お客様に大変満足頂いた事例となります。
医療機器用ホルダー
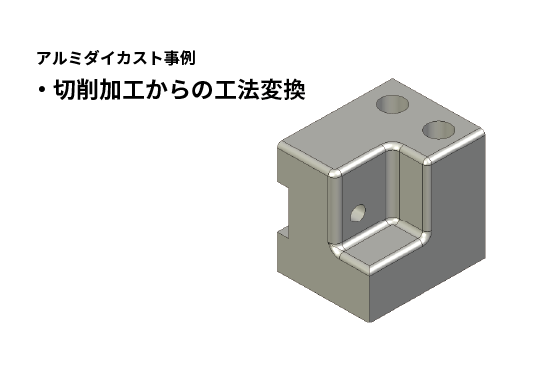
こちらは、医療機器に使用されるホルダー部品であり、従来は切削加工により製作を行なっておりました。しかし、当事例のお客様は、コストに課題を抱えていました。そこで、特許製法ダイカストカセットシステムに強みを持つ当社にお声かけいただきました。当社にて特許製法ダイカストカセットシステムへの工法転換のご提案を行いました。その結果、50%の大幅なコストダウンに成功しました。さらに、ダイカスト鋳造での肉盗み形状への変更により併せて軽量化を実現しました。
電子機器用ケース
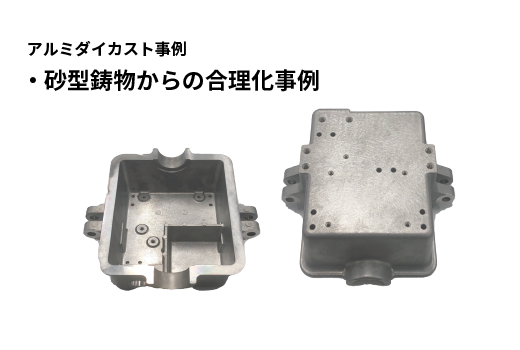
当製品は電流測定用の筐体です。砂型鋳造から特許製法のダイカスト加工に工法変換した事例となります。当事例のお客様は、ダイカストへの工法変換を検討されていましたが、年400個という小ロットであるため金型費用が割りに合わず、工法転換を断念されていました。そこで、当社は特許製法であるダイカストカセットシステムによる生産をご提案しました。当社の特許製法であるダイカストカセットシステムでは、従来のダイカスト金型と異なり、キャビティーのみの製作となり金型費用を1/2に低減できますので、小ロットでも十分に投資回収が可能な製法です。このダイカストへの工法変換により、30%のコストダウンを実現しただけでなく、製造リードタイムも50%短縮することができました。さらに、薄肉化による軽量化も併せて実現しました。
搬送機器用プレート
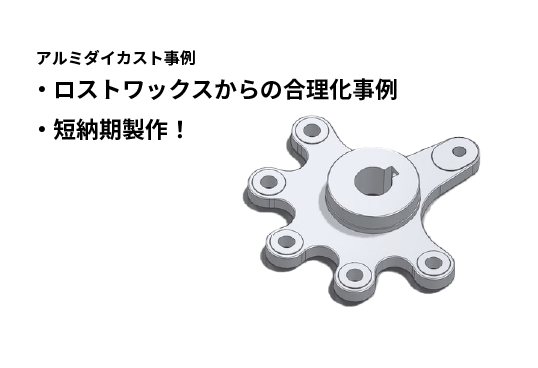
搬送機器に使用されるプレートについて、お客様よりロストワックスでの検討依頼がありました。当プレートは新製品に使用される部品でしたが、立ち上げ時期が4か月後であり、短納期にて量産化する必要がありました。当初、お客様より強度の観点から鉄SS41にて製造したいというご要望をお聞きしていましたが、ご要望の機械的性質をアルミでも満たせることから、量産までのリードタイムを短縮できるダイカストにて製造することを提案しました。
自動車用アダプタープレート
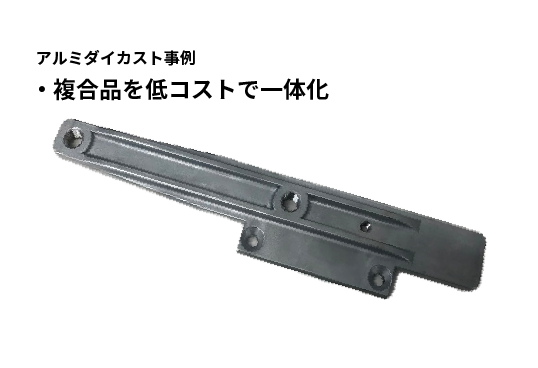
自動車に搭載されるアダプタープレートの生産工程を組立品から特許製法のダイカストに工法変換した事例です。
従来アダプタープレートは、SUS製板金部品と両端丸型平行キーをビスにより接合していましたが、2部品の製作時間とビスによる組立工数が必要となり、コスト上昇及び製造リードタイムの長期化が問題となっていました。生産工程の変更により、コストダウンを実現することを目指し、複数の受託加工メーカー様にお声かけされましたが、ベストな生産方法が見つけられず、切削~砂型鋳造・ダイカストまで提案可能な当社にお声かけ頂きました。
関連情報はこちら
コラム内検索
関連記事
-
2024.11.24 ダイカストについて
アルミダイカストとアルマイト加工
今回のコラムでは、アルマイト加工について説明していこうと思います。 アルマイト加工って、アルミニウムやその合金の表面に酸化皮膜を作る処理のことなんです。この処理をすることで、耐食性や耐摩耗性がアップする上に、見た目もキレイになるんですね。 […more] -
2024.11.24 ダイカストについて
アルミダイカストにおけるコストダウンのポイント
アルミダイカストを用いることで、大幅なコストダウンを実現できる可能性があります。では、コストダウンを実現するためにはどんなポイントがあるのでしょうか? 3つのポイント アルミダイカストに関して、コストダウンを実現するためには大きく3つのポイ[…more] -
2024.11.24 ダイカストについて
アルミダイカストに使用される合金:ADC12
ADC12はアルミニウム合金の一種で、特に鋳造でよく使われている材料です。 主にアルミニウムに銅を混ぜて作られていて、強度、耐食性、鋳造性に優れているんです。 自動車部品や電子機器のハウジングなど、様々な産業で活躍しています。 ADC12の[…more]